Whether you are a microbrewery, a medium brewery or a large one, we can assist you throughout the whole beer bottling process. In fact, we deliver scaled beer bottling plants on the base of your actual needs to ensure you the utmost performance.
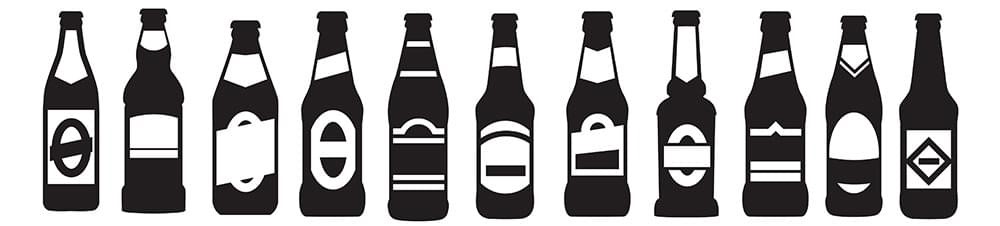
When performed on a professional level, the beer bottling process requires adequate equipment and machines to guarantee:
- Time saving
- Professional results
- Maximum hygiene
Comac Group stands on the market with a complete series of beer bottling machines, designed to suit the needs of small, medium and large breweries. The standard units include automatic beer bottling machines for:
- Microbreweries
- Small and medium breweries
- Medium and large breweries
- Large breweries
Despite the differences due to the size and the performance rate, all Comac’s bottling beer equipments are realized with three systems that complete the beer bottling process:
- The rinsing system, to clean up the bottles before they are filled
- The filling system, to pour the beverage into the bottles
- The capping system, to seal the bottles after the filling
Beer bottling machines and equipment
Let’s discover some of Comac’s beer bottling equipment.
Automatic beer bottling systems for small and medium breweries
Sagitta 12-16-3 P
Simple and easy to use, this beer bottling machine is compact in size and perform the rinsing cycle, the filling and the capping of the beer. Sagitta 12-16-3 P can bottle up to 6.000 BPH and can be customized according to customers’ requests.
Sagitta 12-12-1 P
This beer bottling machine can reach up to 3.000 BPH and is a monoblock for glass bottles based on back-pressure filling technology, suitable for filling both carbonated and still beverages. Sagitta 12-12-1 P offers dedicated recipes for different types of products, adjustable and selectable by HMI.
Automatic beer bottling system for large breweries
Master PET
Master PET is based on back pressure filling technology and is suitable for carbonated and still drinks in PET bottles. This beer bottling machine can bottle up to 70.000 BPH and is realized in collaboration with CFT Group.
Master RS Glass/PET
MASTER RS GLASS/PET can reach up to 90.000 BPH and is based on back pressure filling technology. It is suitable for filling carbonated and still beverages into glass and PET bottles. This beer bottling machine is realized with CFT Group and is the result of advanced research and development.
Discover all our beer bottling equipment!
Which beer bottling plant do you need?
All the steps of the bottling beer process and suggested equipment
#1 Depalletizing
It is the first step in beer bottling and involves the removal of bottles from the original pallet packaging from the manufacturer. After the removal, the bottles are rinsed using filtered water, air or oxygen to aid in reducing the amount of oxygen in them, thus making them ready for process.
To take the next steps you can easily add our conveyors to your bottling line and continuing bottling your beer.
#2 Beer bottling: filling
It is the second stage in beer bottling. Refilling of the bottle with beer depends on the type of the machine: the capacity of the bottles that the machine can accommodate and the speed at which the filler can fill the bottles. After depalletization, the bottles are loaded into the beer bottling machine. At this stage, the bottles are filled with beer and then some amount of inert gases.
#3 Capping
Beer bottling also involves the capping process whereby the already filled bottles are run through a capping machine that seals them with the cap. This capping process is also dependent on the type of the beer filling machine. If the filling machine has a high speed with a large capacity of bottles, then the capping machine will also have the same feature. However, in some beer bottling processes, the bottles are sealed with a cork and bottle cage.
#4 Labelling
The last step of beer bottling is beer labelling. In this process, the already packed and sealed beer bottles are run through a labelling machine, called the labeler. This process is vital since it ensures that all the bottles have the date of manufacture and expiry, which is a requirement for all manufacturers by the standardization organ of any state, to ensure that the health of the citizens is safeguarded.
The process of beer bottling is then concluded by the packaging of the certified beer bottles into the crates or cartons for transportation to the store or market, ready for consumption or exportation to foreign countries.
Beer blotting plants: the units to carry out all the processes
Deaeration, carbonation, pasteurization, packaging, addition of sugar or syrup, heating or cooling are steps that take place during a beer bottling process and are carried out by different components, such as:
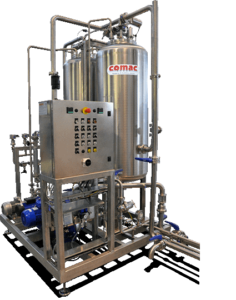
Saturation unit
Deaeration of the water and carbonation are carried out by the saturation unit, a solid AISI 304 stainless steel structure, on which the deaeration tank, the carbonation device and the stabilization/storage tank are anchored.
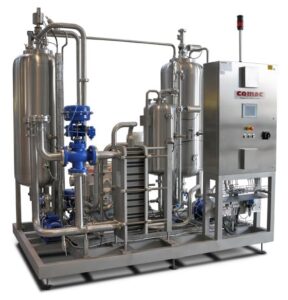
Premix unit
The premix unit is used to deaerate water, add syrup and carbonate in order to obtatin a carbonated beverage. It is made of a solid stainless steel AISI 304 structure, glass beads blasted and treated with protective varnish on which the various devices, such as the deaeration tank, the syrup tank, the mixing water/syrup unit, the carbonation device and the stabilization/storage tank are anchored.
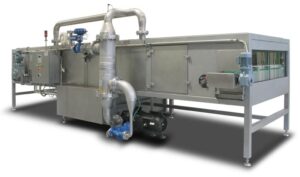
Heating and cooling tunnel
Heating and cooling tunnel brings to room temperature the packaged bottles, either cold or hot. Both units are made of stainless steel AISI 304, and equipped with devices that aim at keeping constant the water temperature.
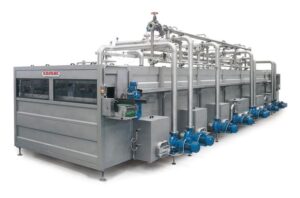
Tunnel pasteurizer
Available in different sizes depending on the needs, this unit comes into the beer bottling process to pasteurize already packaged product. It consists of a stainless steel AISI 304 solid structure that is subjected to an abrasive blasting and protective coating.
If you are planning to take beer bottling to a professional level or to renovate your bottling equipment, Comac can help you: feel free to contact us for any suggestion and information!